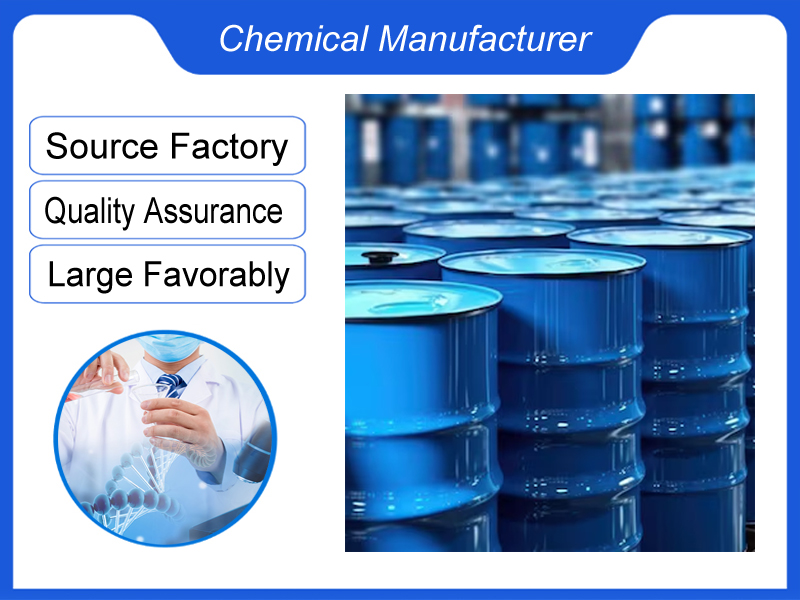
acrylic resin
Category:Paint chemicals
Introduction
Multi-purpose solid acrylic resins are homopolymers or copolymers synthesized through polymerization of one or more monomer raw materials with different characteristics and uses. Monomer raw materials include methacrylates, acrylates and other monomers.
These homopolymers or copolymers, present as beads, powders, granules, microparticles, or melts. The variability in molecular structure makes them adjustable in application, compatible with a variety of film-forming resins, such as chlorinated rubber, chloroacetate copolymer resin, nitrocellulose, vinyl butyl cellulose, etc., and a variety of plasticizers, with excellent biocompatibility, as well as outstanding weathering, durability and other properties.
Acrylic Resin: Characteristics and Industrial Applications
Table 1: Types of Acrylic Resins and Their Properties
Type | Key Characteristics | Typical Applications |
---|---|---|
Thermoplastic Acrylic | Reversible, soluble in solvents | Automotive coatings, adhesives |
Thermosetting Acrylic | Cross-linked, heat-resistant | Industrial finishes, appliance coatings |
Waterborne Acrylic | Low VOC, eco-friendly | Architectural paints, wood finishes |
UV-Curable Acrylic | Fast curing, energy-efficient | Electronics, 3D printing |
Solventborne Acrylic | High durability, weather-resistant | Marine coatings, exterior paints |
Table 2: Key Physical and Chemical Properties
Property | Typical Value | Significance |
---|---|---|
Glass Transition Temp. | 20-120°C | Determines flexibility/hardness |
Density (g/cm³) | 1.05-1.20 | Affects coating coverage |
Tensile Strength (MPa) | 30-80 | Indicates mechanical strength |
Weather Resistance | Excellent | Suitable for outdoor applications |
Chemical Resistance | Good to excellent | Resists acids, alkalis, solvents |
Table 3: Comparison with Other Resin Types
Resin Type | Advantages | Disadvantages |
---|---|---|
Acrylic | UV stable, color retention | Lower chemical resistance than epoxy |
Epoxy | Superior adhesion, chemical resistance | Poor UV stability |
Polyurethane | Excellent abrasion resistance | Higher cost, moisture sensitivity |
Alkyd | Good flow, low cost | Yellowing, poor weather resistance |
Table 4: Major Application Areas
Industry | Applications | Benefits Provided |
---|---|---|
Coatings | Automotive, architectural | Durability, gloss retention |
Adhesives | Pressure-sensitive, laminates | Flexibility, bonding strength |
Plastics | Signage, displays | Clarity, impact resistance |
Textiles | Fabric coatings | Soft feel, wash durability |
Electronics | Encapsulants, displays | Optical clarity, electrical insulation |
Table 5: Environmental and Safety Considerations
Factor | Status | Regulatory Notes |
---|---|---|
VOC Content | Low (waterborne types) | Complies with EPA regulations |
Toxicity | Generally low | Non-carcinogenic |
Flammability | Moderate (solvent types) | Requires proper ventilation |
Biodegradability | Poor (but recyclable) | Incineration with energy recovery |
Acrylic resins offer exceptional versatility with their balance of durability, clarity, and weather resistance. They dominate in coatings and adhesives markets due to their excellent UV stability and aesthetic qualities. While they may not match epoxies in chemical resistance or polyurethanes in toughness, their overall performance makes them indispensable in numerous industries. Environmental regulations are driving innovation toward waterborne and UV-curable formulations.